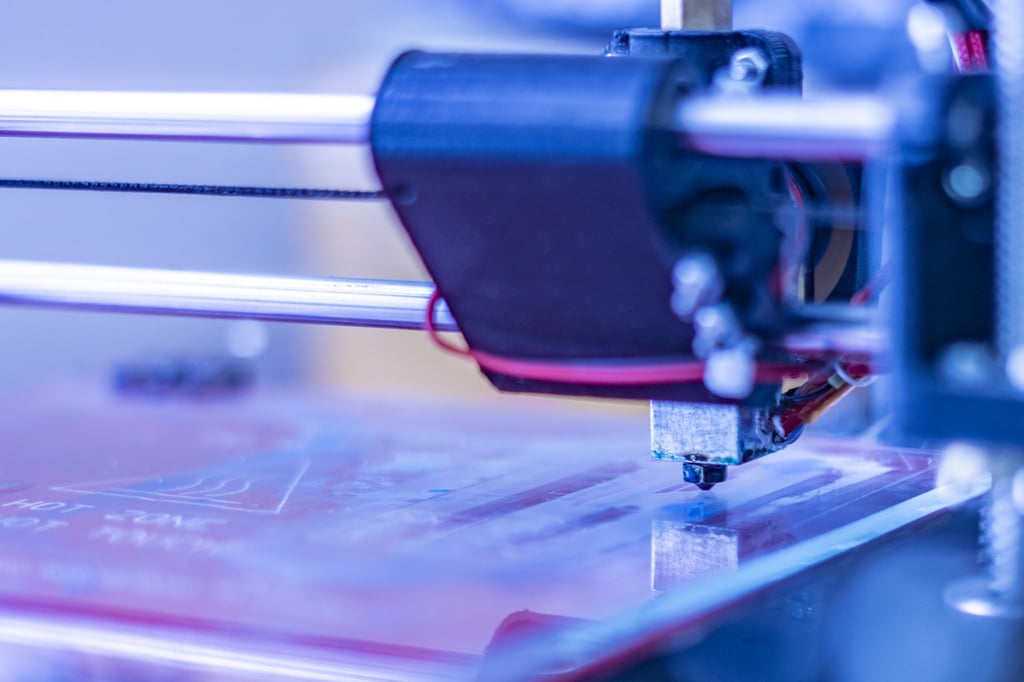
Leveraging advanced technology solutions
Every day, a growing number of industries – from transportation and healthcare to oil and gas – are unlocking new potential with additive manufacturing, also known as 3D printing. This advanced technology offers your organisation a unique pathway to excel in manufacturing innovation. It provides the freedom to design more efficient and effective components, while also enabling you to produce parts locally, anywhere in the world. To help you mitigate risk and ensure safe, reliable parts, we provide a range of specialised certification and training services.
Our additive manufacturing services
As you leverage the transformative capabilities of additive manufacturing, the assurance of quality and safety in your parts and materials becomes increasingly critical. We offer a suite of certification and advisory services, as well as training courses specifically designed for additive manufactured parts and materials. We also offer quality management system certification that helps demonstrate your commitment to industry-recognised standards. All of these are delivered by our team of highly skilled inspectors who are leaders in their field. They'll work with you to understand the unique challenges of your business, delivering actionable insights grounded in real-world experience to help you mitigate risk.
Part certification
Ensure parts meet industrial requirements for quality, safety and consistency.
Material certification
Certify feedstock with witnessed testing and material specification assessments.
Facility advisory
Implement facility processes that comply with international standards and best practices.
Facility qualification
Receive Additive Manufacturing Quality (AMQ) scheme approval through expert facility audits and process reviews.
Training
Understand the requirements of additive manufacturing certification and facility qualification.
Why work with us?
Global reach, local insight
LRQA offers specialist inspection and assurance services in over 80 countries. Whatever your sector, we can help you anticipate, mitigate and manage additive manufacturing risks. Our team of over 1,000 inspection experts use extensive local sector knowledge to help thousands of clients safely and sustainably establish best practices.
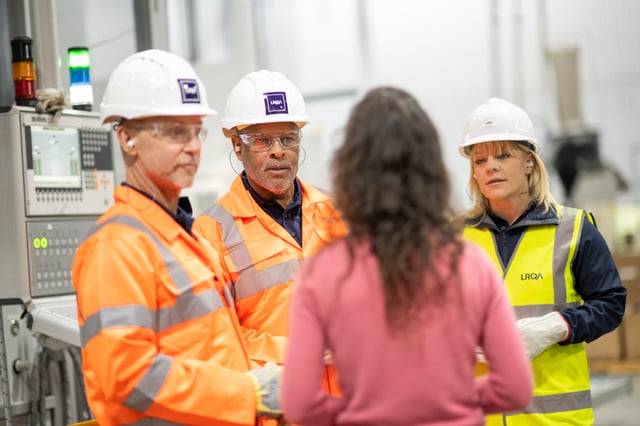
Consistent approach
We work side-by-side with you, listening first to gain a comprehensive understanding of your business including its risks, challenges, and needs. Using our broad expertise, we’ll help you identify areas that need improvement before creating solutions that will support your business and optimise your additive manufacturing assurance programme.
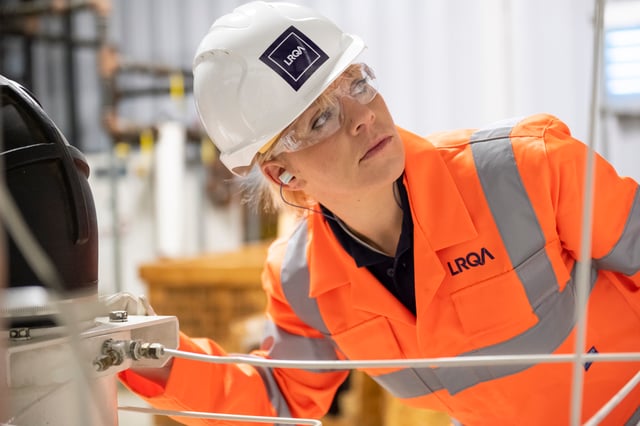
Flexible delivery
In most cases, we can deliver our additive manufacturing services on-site or remotely, using safe and secure technology. If you opt for our remote delivery methods, you’ll receive the same high-quality service with the added benefit of flexibility, fast delivery, and access to global expertise.
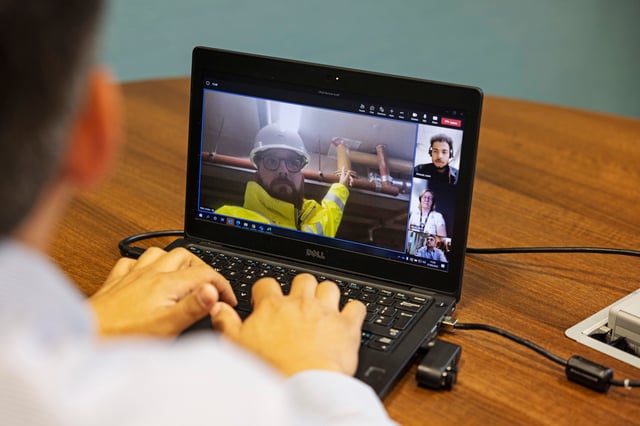
From small manufacturers to world-leading brands
We have a long history of delivering tailored inspection and additive manufacturing services to businesses of all sizes across multiple industries. Our inspectors, specialists and project managers are internationally certified with extensive sector-specific experience, so you can be confident that we will offer real, actionable insights that drive growth.
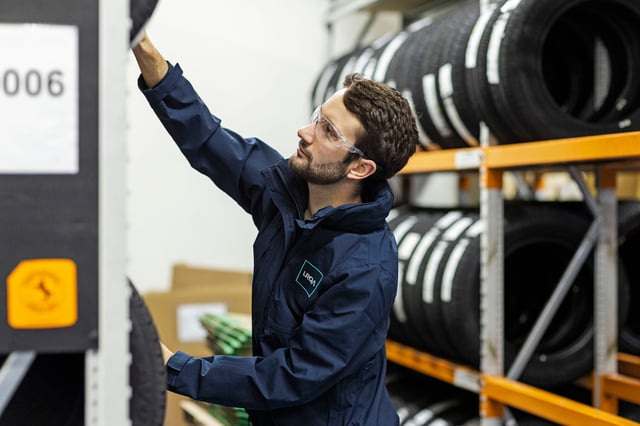
Frequently Asked Questions
What is part certification?
Overview
While additive manufacturing (AM) grows at a rapid pace, there was previously no standardised way of proving to manufacturers and regulators that AM products are safe.
AM techniques give companies flexibility to design innovative products and/or reduce production lead times, but there are still significant barriers to overcome to ensure consistent quality and safety. To compound this issue, there were no global certification schemes that took into account AM-produced parts.
This is why LRQA and industry partner TWI have introduced a broad-based, AM part certification service that spans multiple industries and applications, from general manufacturing, to oil and gas upstream and downstream.
How it works
We help manufacturers of AM parts prove to their customers and the market that their parts meet the required codes, standards, controls and best practices. We apply evolving international standards on AM, setting the requirements to prove equivalence with existing manufacturing methods, codes and standards, and apply our knowledge to help develop international standards on AM.
When we work with clients to certify their AM parts, we look at not only their designs but their material choice and supplier, as well as the AM facility they'll use. We do this through our framework. We can also help train personnel on the qualification and certification of AM-related facilities, materials, and components.
What is material certification?
Overview
Existing metallic materials standards haven't yet expanded to include requirements for the additive manufacturing material form, and the required tests and acceptable tolerances for other material forms can't simply be adopted because of differences in the resulting properties. This requires tailored test plans that are carefully designed and performed to prove the suitability of the formed material.
Consistency is crucial for additive manufacturing. That begins with control and characterisation of the feedstock - powder or wire, for example. Chemical composition, particle size distribution, apparent and tap density, are just a few basic characteristics of metallic powder that need to be properly tested and controlled. This doesn't only apply when you're purchasing powder from a supplier, but any variations that may occur between batches (virgin and recycled) must be accounted for.
The storage and handling of the feedstock must also be controlled to an approved procedure, in a similar fashion to welding consumables. This is to avoid contamination, physical damage, oxidation, and ignition/explosion of the feedstock.
How it works
We help manufacturers of AM materials prove to their customers and the market that the materials produced comply with the associated material specifications and best practices. We use our framework, so we apply evolving international standards on AM and set the requirements to prove equivalence with existing manufacturing methods, codes and standards. Compliance with our certification framework enables manufacturers to issue Type 3.1 or Type 3.2 certification for the materials.
What is facility advisory?
Overview
A robust control process, encompassing everything from design and manufacturing planning to raw material procurement, recycling, manufacturing, post-processing, inspection, and final acceptance, is pivotal for producing high-quality and consistent AM products. Such a process is crucial for scaled production. Without these controls in place, an AM facility may struggle to remain competitive, especially given the intensifying market competition and evolving standards and regulations.
LRQA’s AM Facility Advisory service equips both existing and new facilities with the tools and insights needed to commence production effectively. Drawing from our extensive experience in qualifying AM facilities globally and our active participation in international standards committees, we guide facilities in aligning their processes with international best practices, while also recognising and accommodating the unique characteristics of each facility.
How it works
Our team of experts follows clearly defined phases and timelines to ensure minimum disruption to a facility’s daily operation. Depending on your unique requirements, activities may include the following:
- A Gap analysis to map out the required scope and documents for the facility. An onsite demonstration audit can be also conducted.
- Procedure development where LRQA create the procedures, work instructions, record templates, and/or inspection and test plans. At the end of the process, the AM facility receives the full set of facility documents ready to be formalised and audited against the specified standards and requirements.
What is facility qualification?
Overview
Even with well-designed parts with approved materials, many things can go wrong at the production stage. When first adopting technology, companies either set up new in-house additive manufacturing facilities, or outsource to AM service bureaus to produce their components.
In both cases, independent qualification by LRQA can prove to your clients that you have appropriate processes in place.
How it works
Using our framework, for metal- based AM processes and “LRQA Guidance Notes for Polymer AM Certification” for polymer-based AM processes, we fully audit printing facilities, examining the following areas:
- Personnel competence
- Control of feedstock, auxiliary materials (e.g. gases, cleaning materials) and part handling
- Installation, maintenance and ongoing capability of the AM system
- Control of manufacturing through facility procedures and manufacturing plan.
LRQA has qualified AM facilities that utilise powder-bed fusion and direct energy deposition techniques.