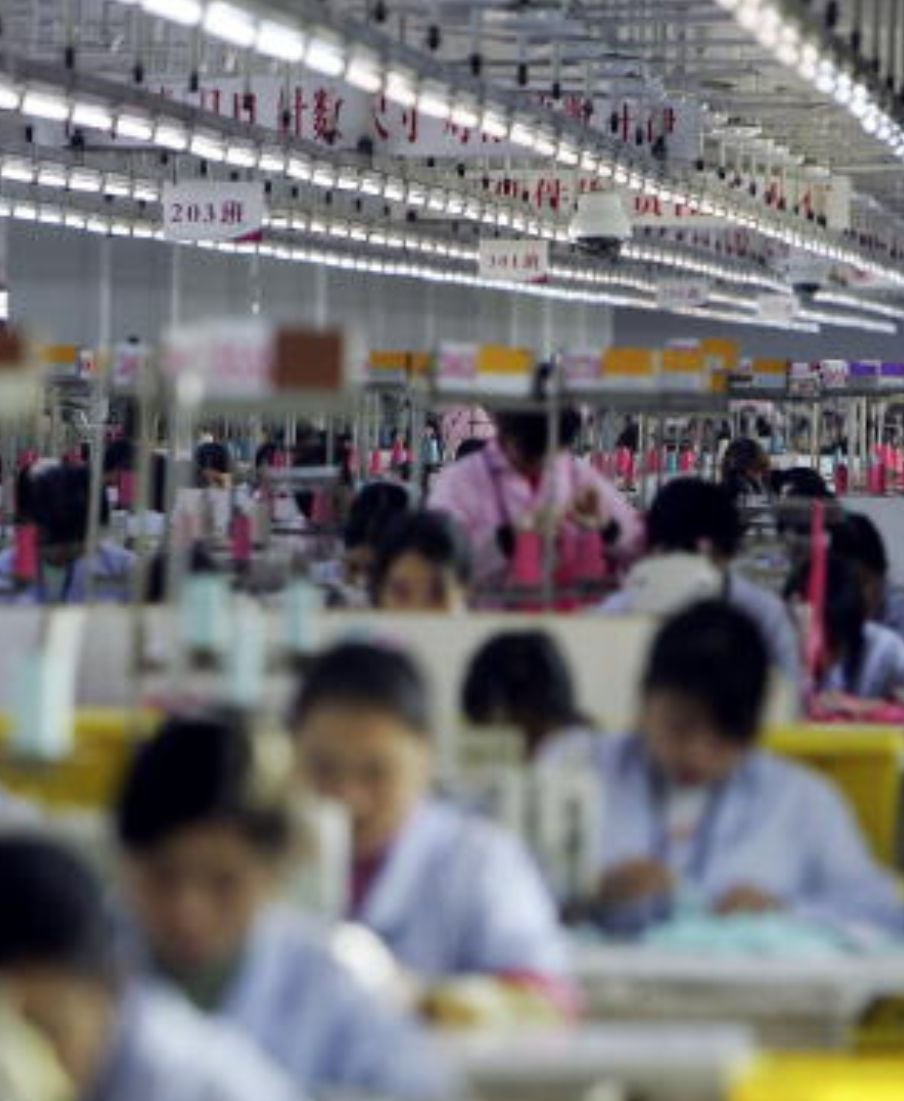
Waste and emissions supply chain engagement
Driving improvements in waste and emissions across supply chains
Improve waste management in supply chains
Waste is a key sustainability and business issue for the apparel and footwear sector who are resource-intensive, relying on large amounts of water, energy, and raw materials. Textiles in landfill can release methane, a potent greenhouse gas, and dyes and chemicals can leach into soil and water.
Waste also represents a loss of economic value. Materials that could be reused or recycled are instead discarded, representing a missed opportunity for additional revenue or cost savings.
As regulations and expectations around waste management increase, the importance of waste management for apparel and footwear companies will only increase.
For brands and buyers, waste is a key issue in supply chains. Driving improvements can be challenging, especially when supply chains are vast, remote and when leverage can be limited.
For suppliers and factories, time, access to resources and know-how can be a challenge.
Footwear and apparel factory waste management approach
LRQA is helping apparel and footwear companies dramatically improve waste management in supply chains through a specialised on-site capacity building program. Our team, deploying custom tools and deep expertise, goes on site to measure baseline performance and engage with site management to establish sustainable systems for waste management. In partnership with the Footwear Distributors and Retailers of America (FDRA) and the Apparel Impact Institute (Aii), we also deliver measurable, enduring impact for many of the world’s top brands and manufacturers.
Waste diversion
In a batch of 34 factories in China, waste diversion rates were increased from an average of 69% to 100% in less than a year.
Waste recycling
In a batch of 12 factories in Vietnam, waste recycling rates were increased from an average of 54% to 64% in less than a year.
Emissions
For a group of 46 factories across China and Vietnam, 9779 annual MTCO2 emissions were avoided through improved waste reuse and recycling.
Zero waste management
76% of participating factories’ Zero Waste Management systems have been improved to A or B grade.
Positive income stream
In one factory, our efforts saw waste management transformed from a business expense of RMB 44,000 into a positive income stream of RMB 13,000.
Implementation: Waste & Emissions Supply Chain Engagement guide
Download guide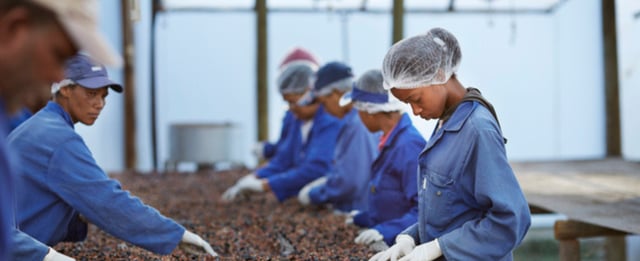
Why partner with us?
We bring to every project our deep expertise in supply chain due diligence regulations, international best practice, a thorough understanding of risk exposure and risk management, and insights into industry practices and investor expectations.
Aligned with evolving requirements
Our methodology is updated regularly to align with legislation and industry standards.
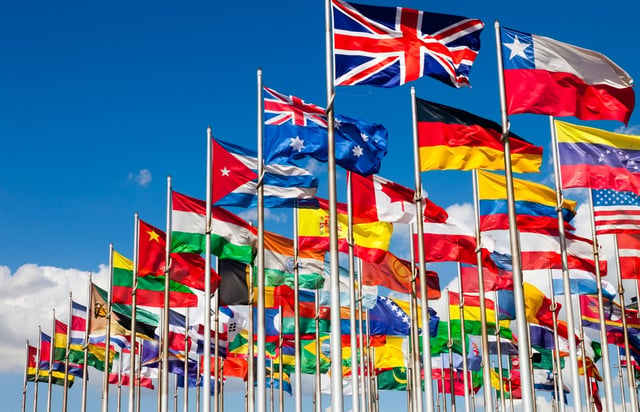
Tested and refined
Our methodology has been applied over decades with hundreds of companies around the world. We provide pragmatic, resource effective solutions that can be both implemented and scaled.
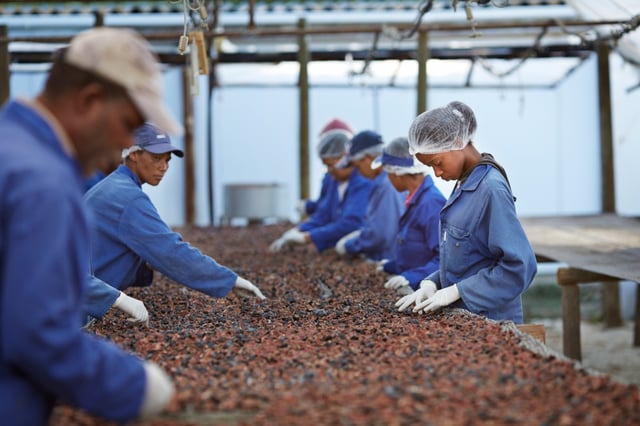
Based on end-to-end expertise
Our proprietary research and analytic tools are used daily around the world to identify risks, hear from workers directly, and are tailored to industry and geography.
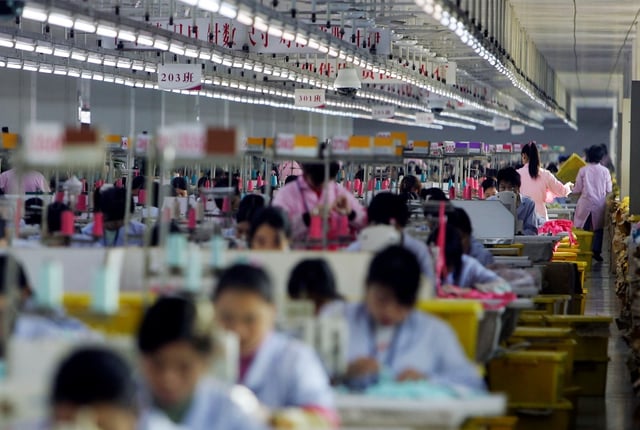
We are efficient and action orientated
We know what to look for, delivering you and your teams the insight required quickly and efficiently.
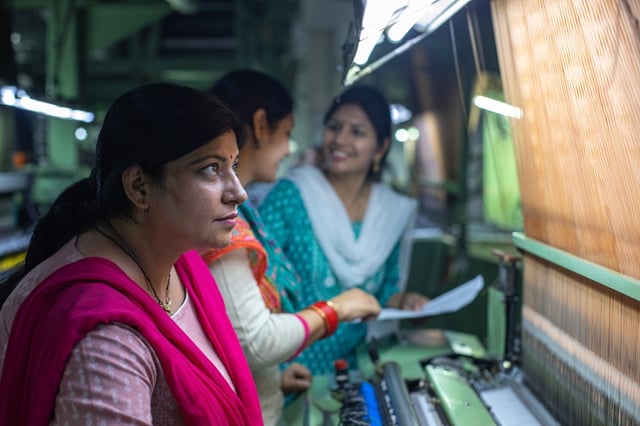
Related solutions
Explore our Consulting Services portfolio and find out how we can partner with you to solve ESG challenges