Continuing in our series of pressure equipment industry chats, we sat down with two leaders from Graham Hart (Process Technology) Ltd (GHPT).
Continuing in our series of chats with members of the pressure vessel industry, we sat down with Chris Hart and Charles Byrne from Graham Hart (Process Technology) Ltd. recently.
Chris is GHPT's managing director; Charles is its technical director. Speaking at their offices in Bradford, they discussed pressure vessel business in general, pressure testing safety, as well as the direction of the Pressure Vessel Manufacturers Forum, an industry group facilitated by LRQA that aims to provide a collective voice for pressure vessel manufacturers.
How long have you been a member of the PVMF?
Chris: From the very early days. We started attending from the second meeting in 2011, which was held in Lincoln with about 10 companies, and we have attended every meeting since. Today there are now 19 companies involved in the PVMF. LRQA approached us and asked if we would like to join likeminded companies. Initially, thoughts of being in the same room as our competitors meant we felt quite apprehensive and we were slightly guarded. However, we soon realised that all the organisations had common struggles with the interpretation and application of regulations, lack of training and skills. Recruitment of professionally qualified staff for the industry was and still is a nationwide industry issue. Discussing common issues that aren’t competitive has become the norm.
What success have you seen the forum achieve?
Charles: We believe that the first achievement of the PVMF was our ability to contribute to (and influence) the decision to retain PD5500 (Specification for unfired, fusion welded pressure vessels - editor). The standard which was written and maintained by BSI was under threat of being deleted. BSI attended meetings to listen to discussions amongst the manufacturers about the use of the standard and it was soon realised that PD5500 was still being widely used and like any standard just needed updating.
BSI are now an affiliate member of the PVMF and regularly attend meetings to discuss codes and standards issues which affect most UK manufacturers.
Manufacturers are now seen as a group who use their initiative to engage with regulatory bodies and therefore become part of the process and the solutions going forwards.
The PVMF meetings have also been of great commercial benefit to many of the members. In 2014 following a presentation about R&D tax relief, several members went on to secure refunds in taxes from the government worth tens of thousands of pounds. Also, discussions relating to commercial terms and contracts have been enlightening.
Chris: Networking with our industry colleagues has helped us to develop a greater understanding of the markets we work in, both nationally and internationally. This has enabled us to focus our activities and involvements around the areas that seem most likely to deliver results in the short and medium term.
Trusting in your industry sector is key and when the members started to trust each other as manufacturers, the PVMF started to work well.
Charles Byrne (left) and Chris Hart (right)
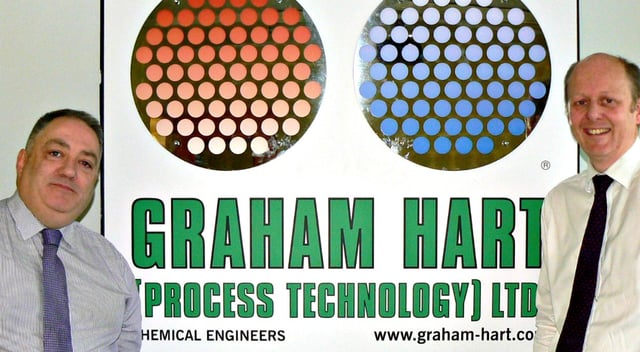
Pressure testing safety is a hot topic for members of the PVMF. Why is this?
Charles: Representatives from LRQA attend every meeting. As part of their role LRQA surveyors report safety observations to both the client in case work needs to be stopped for safety concerns and for their own H&S system. At the start of each meeting there is a ‘Safety Moment’ and it is through these safety moments unsafe practices have been identified. Members have also been able to contribute their own safety moment with things they had heard and seen (officially and unofficially) at sites throughout the UK. This gave the impression that pressure test failures and potential dangerous situations were on the rise.
Manufacturing safety observations on site weren’t being reported to HSE. The amount of injuries was not being made publicly available. As manufacturers we questioned the HSE and the IMechE Pressure Systems Group (PSG) about this. The word started to spread about what we were trying to achieve as a group and more people got in touch with PVMF about the number of incidents. Site operators were getting in touch to find out what could be done. It is still known as a ‘dirty subject’ though. No one wanted to say, ‘I’ve had a problem with pressure testing safety on my site but I’m not sure what to do’.
It is still known as a 'dirty subject' though. No one wanted to say, ‘I’ve had a problem with pressure testing safety on my site but I’m not sure what to do’.
The PVMF put forward an initiative to the PSG (supported by LRQA) which was also supported by HSE and other bodies in the pressure equipment industry to highlight unsafe practices when pressure testing. But it’s only now that the true extent of the problem is only being recognised. This became more evident following the Pressure Testing Safety Seminar which was held in London in December 2017. After which several delegates approached members of the PVMF to talk about the subject. This was the first event jointly run by the PVMF and the IMechE PSG.
Chris: Complacency, when pressure testing is the unseen danger. The common view is that pressure testing safety will not change until there is a major incident and without the PVMF, GHPT could not have put it out there alone.
End users, owners and other interested parties now freely engage and work with the PVMF as a great partnership. Manufacturers are not afraid to lead and contribute.
You represented the PVMF at the IMechE Pressure Testing Safety Seminar at the end of 2017. What has happened in the industry since then?
Charles: The industry certainly sat-up and took notice. More than 100 delegates attended the event in December and there have been many discussions since.
The IMechE PSG has created an industry alert in collaboration with the PVMF, with the first one being issued in October 2018. This document highlighted the absence of standards or programmes for the training, qualifying and certifying of employees for competence levels. It also recommends that manufacturers read document GS4 (HSE Safety Requirements for Pressure Testing - editor) and ascertain how well they follow or adhere to its recommendations.
The pressure equipment industry wants to see people trained, certified, qualified and competent, but a course or qualification does not exist. The content required could take up to 18 months to develop and deliver.
So, in the interim, the PVMF are working on getting the word out to the industry – can they check their systems and review the guidelines of GS4. It’s a straight-forward approach.
How has the landscape of the UK pressure vessel industry changed over the last 7 years?
Chris: The clients/end users have become far more educated in codes, standards and regulations and they know what they want. GHPT have changed internally following the implementation of the F4N route too. We’ve adapted to lean manufacturing to work alongside the client base.
Some end users and owners no longer possess a thermal or mechanical design department within their business. This gives firms like ours the opportunity to offer them a complete design, manufacture and testing service all under one roof.
Our overseas clients have increased significantly by 28% with exports to Iceland, Norway, Pakistan, India, Germany, Ireland on the rise.
The emergence and increased employment of EN13445 is a game changer (EN 13445 applies to unfired pressure vessels subject to internal pressure greater than 0,5 bar(g), but may be used for vessels operating a lower pressure, including vacuum - editor). You can no longer ignore it as more clients are asking for equipment to be manufactured to the standard. In fact, embracing it is the way forward.
On the downside, we’ve seen lots of competitors going out of business. Sadly, some big and famous names. Companies have changed shape with restructures, owners have changed, but it’s still a competitive landscape.
We are a high end, high integrity specialist manufacturer. That’s the bespoke nature of the offering from GHPT. Providing thermal and mechanical design simulation, leak free service – all with an OTIF (On-Time-In-Full) rating of 100% since 2016 (98% 2015, and 95% 2014).
Recruitment for mechanical engineers, production staff and fabricators (welders and machining) has always been difficult in this industry. However, we have great staff and a high retention rate providing us with a real backbone of experience to draw upon. We also have a successful apprenticeship programme that we aim to maintain and increase going forwards.
How do you think Brexit will affect your business, and the broader UK pressure equipment sector?
Charles: Not at all. We have complete confidence in our flexibility to adapt. The PVMF has seats on a number of Boards that provide useful information on the direction of the discussions taking place at government levels. This guidance is being shared with our members and leaves us all well placed and informed to prepare for the next stages beyond March 2019.
About GHPT
Incorporated in 1973, and based in Bradford, GHPT are specialists in the field of heat and mass transfer. GHPT has built up a comprehensive, technology based, design and manufacturing facility providing a full service from process data to completed equipment.
Chris Hart
Chris is the Managing Director of Graham Hart (Process Technology) Ltd. He graduated with a Masters Degree in Chemical Engineering from the University of Bradford in 1998. He started his career in the design and manufacture of combustion equipment for the Chemical, LNG and Energy sectors.
In 2002 he moved to the family business and took over as Managing Director in 2011. In 2016, Chris was asked to Chair the University of Bradford, School of Chemical Engineering, Industrial Advisory Board which meets several times a year to assist the University in forming stronger links with the Chemical Engineering industry and its related professional bodies.
Charles Byrne, CEng FIMechE
Charles has been involved in the pressure equipment industry for more than thirty years and joined GHPT in 1988. His current role as Technical Director enables him to lead developments in the design, fabrication and testing activities for all bespoke pressure equipment.
Charles represents the PVMF in a position of Vice-Chair at the Pressure Systems Group at the IMechE. He also leads up the Pressure Equipment Consultation Forum (PECF) – a body responsible for the interpretation of pressure equipment legislation from a UK point of view. His passion is the development of an inherently strong UK pressure equipment industry that delivers safety and quality through synergy.
About the PVMF
Formed in 2011 the PVMF brings together the UK’s market-leading pressure vessel manufacturers to share resource and industry knowledge both on technical and commercial issues. To provide a collective voice to influence to government, government agencies and standards settings bodies with regards to the engineering manufacturing environment.
Sponsored and facilitated by LRQA, meetings are held several times a year. Topics and subjects discussed are driven by the members and range from engineering issues such as the introduction of or amendment to codes and standard, fabrication techniques and health and safety to recruitment, procurement and commercial concerns.
Membership of the PVMF is a symbol of integrity and commitment to quality. You can learn more here.